Streamline Your Intercultural Workplace: The Power of the 5S Methodology ๐๏ธ
1/28/2025
The other day, while attending a networking event in Detroit's automobile-focused hub, a conversation with one of my networking partners introduced me to the 5S Workplace Organization Methodology. This sparked a thought: how can we leverage this brilliant concept to build intercultural competence?
The 5S methodology, a cornerstone of lean manufacturing, is designed to enhance workplace efficiency, safety, and productivity through five key principles: Sort, Set in Order, Shine, Standardize, and Sustain. Its origins trace back to Henry Ford's CANDO system, which emphasized Cleaning up, Arranging, Neatness, Discipline, and Ongoing improvement. Japanese manufacturers, particularly Toyota, later refined and adapted these ideas, blending them with local practices to create the globally recognized 5S approach to operational excellence.
The development and global adoption of the 5S methodology are prime examples of how cultural exchange drives innovation and progress. Henry Fordโs foundational CANDO system provided the framework, which Japanese manufacturers adapted and elevated to new heights. This intercultural collaboration exemplifies the power of respecting diverse perspectives and blending global insights with local expertise.
For intercultural competence, the 5S story underscores critical skills: openness to collaboration, mutual respect, and the ability to integrate diverse approaches. In todayโs interconnected workplaces, these skills are vital for fostering innovation, enhancing communication, and creating a culture of growth and mutual understanding across cultures.
๐กHave you ever heard about the 5S methodology?
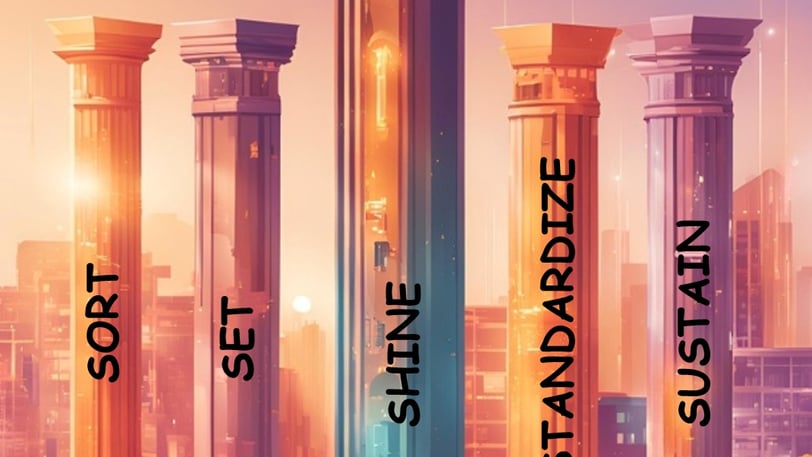

Follow me on
Contact
Connection
DiverseCultureSolutions@aol.com
Mobile: 248-824-4352
ยฉ 2024. All rights reserved.